Consultando le pagine del nostro sito, shop che riguardano il settore monopattini o addirittura digitanto il modello del vostro monopattino su ebay avrete notato che, visto la mole di articoli presenti, il monopattinista è spesso interessato agli upgrade non solo di performance ma bensì anche estetici del suo mezzo. Ebbene si, il mezzo che si utilizza tutti i giorni per andare a lavoro o al bar con gli amici viene visto anche come oggetto da personalizzare, da rendere unico. Quindi perchè non creare una serie di upgrade marchiati “Mi customs”?
L’idea Mi Customs
E’ da tempo che ci siamo posti come obiettivo di creare qualcosa di nostro, qualcosa che ci permettesse di incrociare uno Xiaomi per strada e dire “Ok, è sicuramente un utente che si segue”. Insomma, una gamma “Mi Customs” che faccia riferimento al nostro portale, una serie di prodotti limitati posseduti da una piccola nicchia di utenti che decidono in qualche modo di supportarci, di apprezzare il nostro lavoro. Sin da subito abbiamo capito che la cosa sarebbe stata un lavoraccio: un conto è pubblicare articoli su un blog, ben diverso è invece progettare oggetti funzionali e aver la possibilità di generarli poi da zero.
Creare una gamma di upgrade estetici Mi Customs avendo a disposizione solo uno studio è una cosa abbastanza complessa e che richiede svariate competenze. Fortunatamente siamo nel 2022 e a venirci incontro alla creazione di upgrade estetici, oltre alle svariate ore di studio, è la tecnologia di stampa FDM, ovvero la manifattura additiva. La stampa FDM (modellazione a deposizione fusa) si basa sull’estrusione di materie termoplastiche mediante un ugello riscaldato che fonde il materiale e deposita la plastica, strato dopo strato, su una piattaforma di stampa. Gli strati, generalmente di 0,2/0,3 mm vengono depositati uno alla volta, fino a completamento della parte.
La stampa FDM permette ai maker/artigiani digitali di creare manufatti unici partendo solo da una idea, da uno schizzo. Essa riveste un ruolo importante anche nella prototipazione a livello aziendale e ultimamente anche nel settore aerospaziale.
Ma vediamo ora cosa c’è dietro alla produzione di un parafango ad esempio, oggetto che agli occhi comuni può risultare un banale “pezzo di plastica” ma che in realtà ha tantissimo lavoro dietro.
Fase 1 – Progettazione
Per la progettazione dei parafanghi e cupolino Mi Customs siamo sempre partiti da uno schizzo su carta.
Avere una idea a grandi linee della sagoma del prodotto è essenziale, disegno più o meno sportivo, lunghezza, forma vanno definiti prima di mettersi alla vera e propria progettazione 3d. Tralasciamo di allegare eventuali foto perchè non siamo certi disegnatori nati!
Successivamente siamo passati alla rilevazioni di tutte le misure necessarie. Larghezza e profondità delle viti di fissaggio al monopattino, ampiezza del fanale xiaomi con sedi delle viti stesse, distanza del gancio di chiusura dal telaio del monopattino, arco del parafango stesso per farlo passare il più possibile a filo ruota. Insomma ne siamo usciti con una infinità di numeri, ma è una procedura essenziale per creare un prodotto utilizzabile e per non incappare in continue revisioni del progetto in fasi avanzate.
Fatto questo siamo passati all’ambiente di progettazione 3D vero e proprio tramite software appositi, nel nostro caso Fusion 360. Utilizzare tale programma non è del tutto immediato, per tracciare tutte le forme del parafango occorre disegnare una infinità di schizzi (più di 50!) che verranno poi estrusi e fusi tra di loro per creare dei solidi che daranno forma al nostro risultato finale. Abbiamo perso il conto delle ore di studio passate su Youtube per imparare ad utilizzare le funzioni a noi utili!
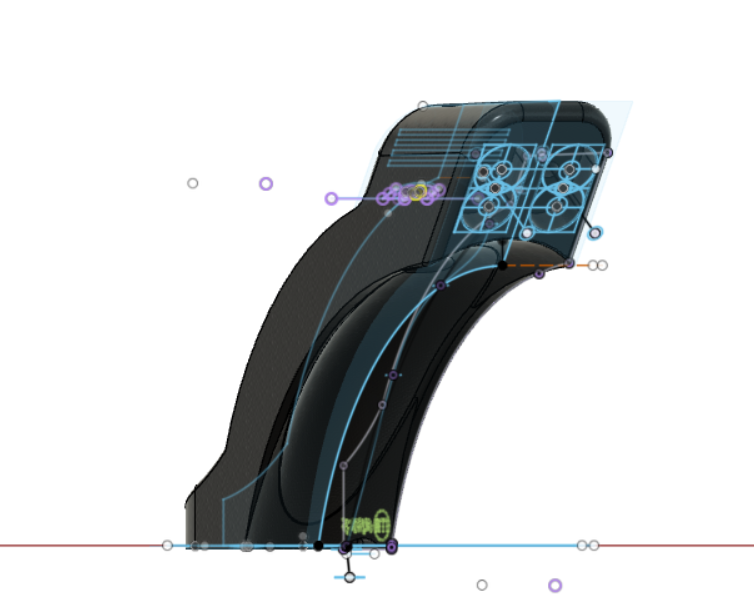
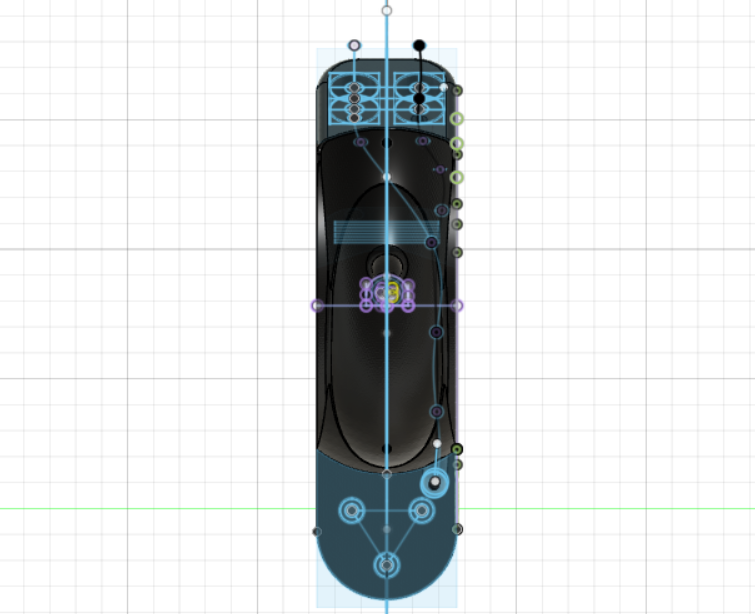
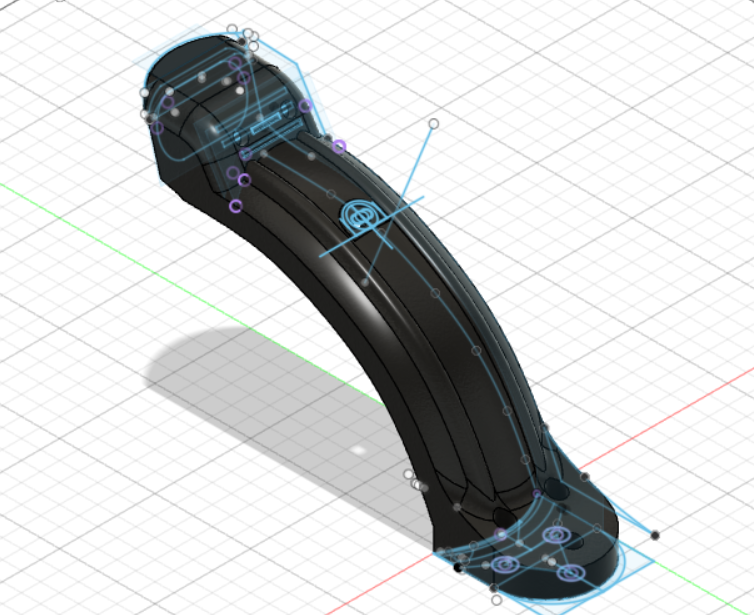
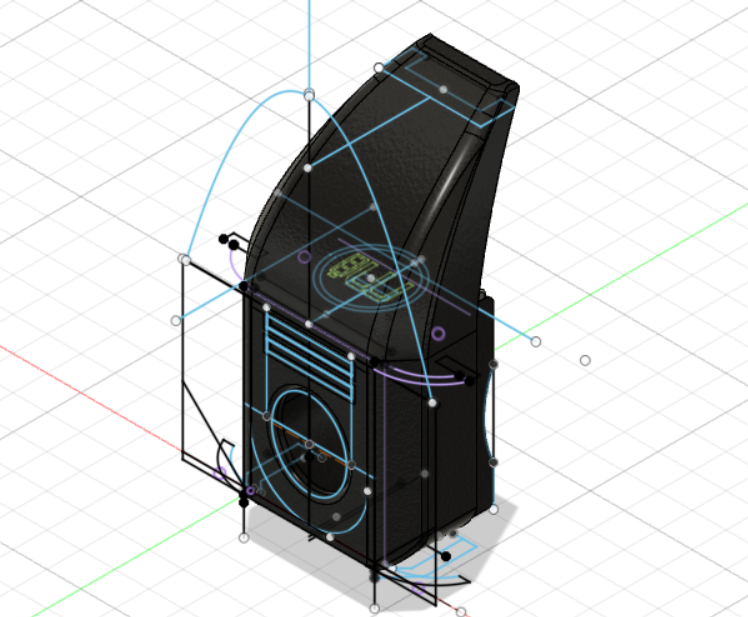
Dettaglio da non trascurare è il disegnare un prodotto che dovrà poi essere stampato in 3D, con tutti i limiti del caso. Dimensioni, angoli di sbalzo, tolleranze, lato da cui far partire la stampa, minor utilizzo (o assente nel nostro caso) di supporti: tutto deve essere studiato per poter poi creare una stampa 3D di qualità, senza troppi artefatti e con una determinata resistenza. Inutile disegnare un prodotto che potrà restare al massimo su uno schermo di un PC, non riproducibile come oggetto fisico.
Abbiamo inoltre dedicato particolare importanza alla gestione dei cavi dei fanali. Odiamo i parafanghi dove l’utente deve cimentarsi in fissaggi con stratagemmi tipo colla a caldo o dove vanno lasciati addirittura semi liberi.
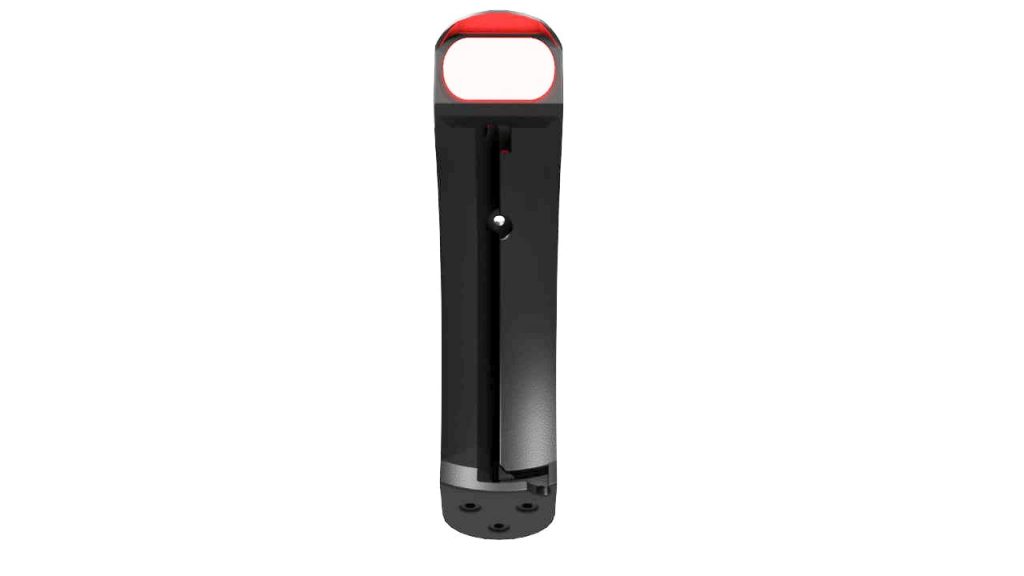
Nel parafango Smooth Single e Dual i cavi passano attraverso un canale ricavato all’interno del parafango stesso.
Tale fase, a tratti veramente stressante, è durata (contando tutte le revisioni in fase d’opera) ben oltre 20 ore a componente. Il prodotto finale è un file STL, un formato standard per i modelli 3D. La geometria 3D è descritta da una mesh di triangoli e le informazioni dimensionali sono contenute in ogni singolo triangolo.
Fase 2 – Rendering
La fase di rendering è la conversione mediante apposito software del profilo di un’immagine bidimensionale (nel nostro caso in un 3D composto da triangoli ovvero il file STL) in un’immagine dall’aspetto realistico e percepibile come tridimensionale, grazie al calcolo accurato della prospettiva e all’aggiunta di colori, luci e ombreggiature.
Questa fase non è del tutto essenziale ma abbiamo preferito non ometterla per avere una idea più realistica del prodotto che saremo andati a stampare.
Il rendering dei prodotti Mi Customs non è stata cosa da poco, i software in gioco sono svariati e per lo più a pagamento (Rhino, Photoshop). In questo caso la spesa non valeva la resa ed inoltre apprendere l’utilizzo di tali programmi ci sarebbe costato varie ore di studio.
Quale è stata quindi la persona a noi più vicina in grado di produrre dei render dei nostri prodotti? Ebbene…un architetto!
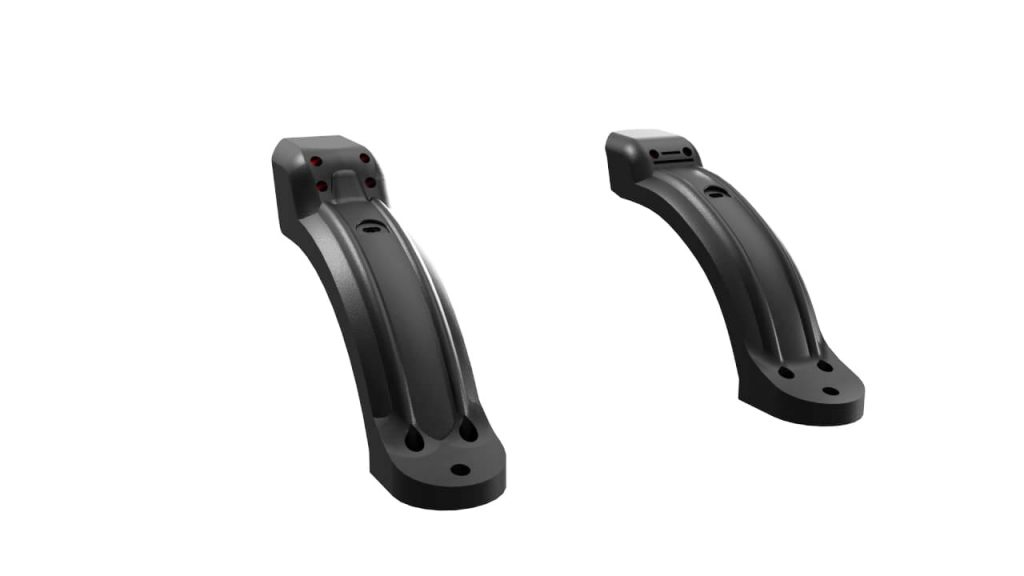
Scelta delle superfici, prospettive, illuminazione: grazie a questo professionista avevamo finalmente davanti i nostri occhi una idea molto veritiera di ciò che stavamo sfornando, il tutto tramite immagini molto qualitative.
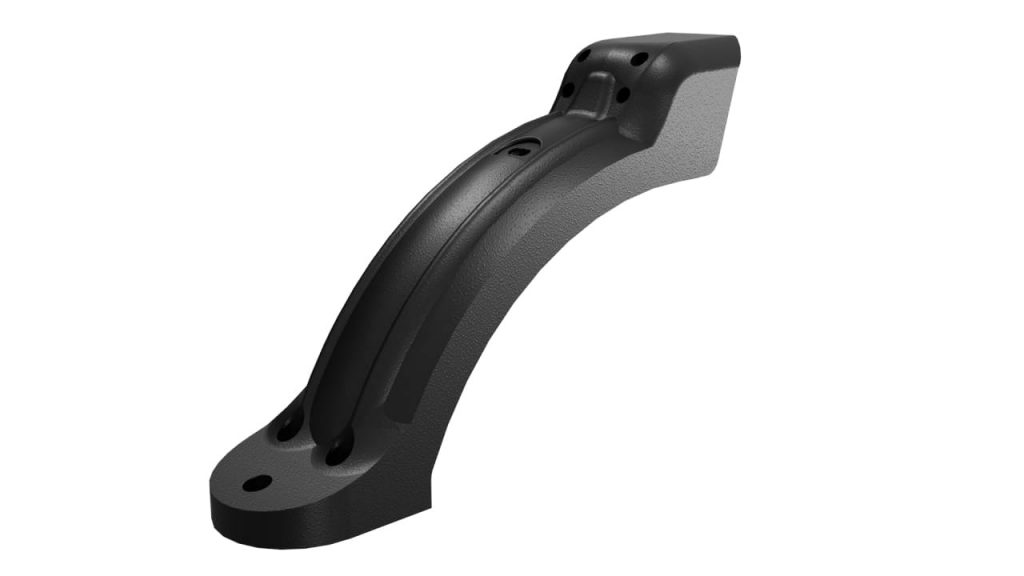
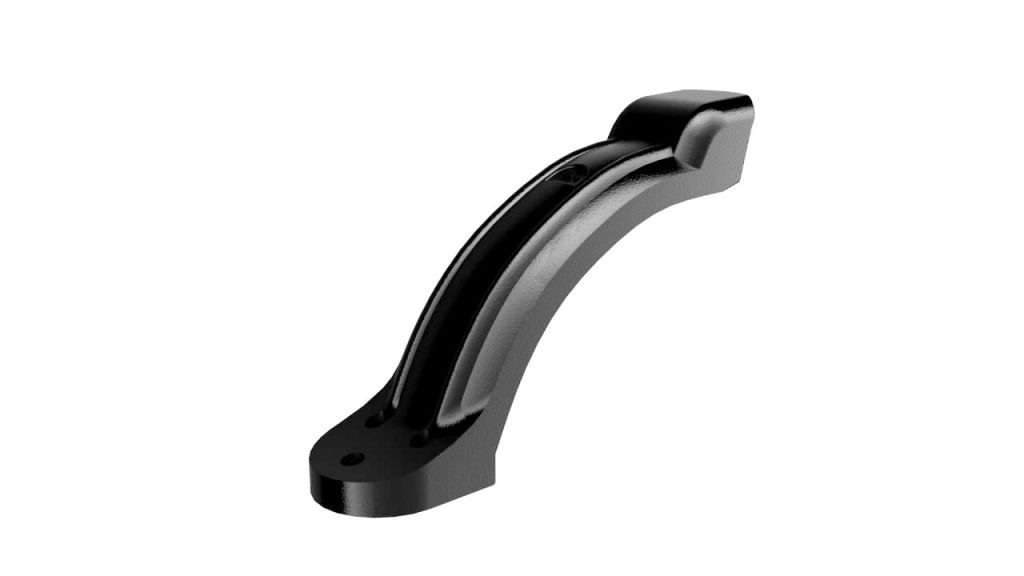
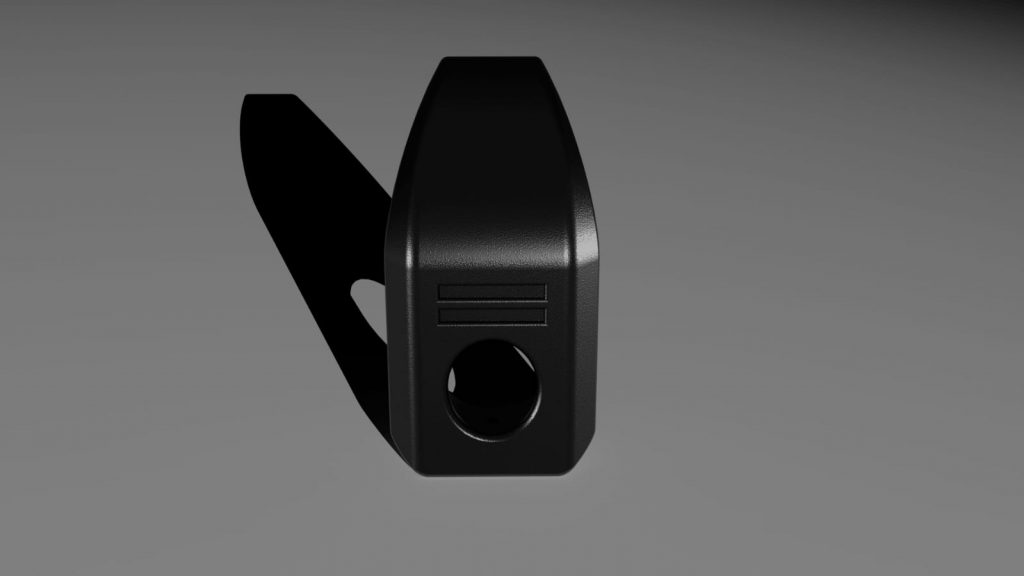
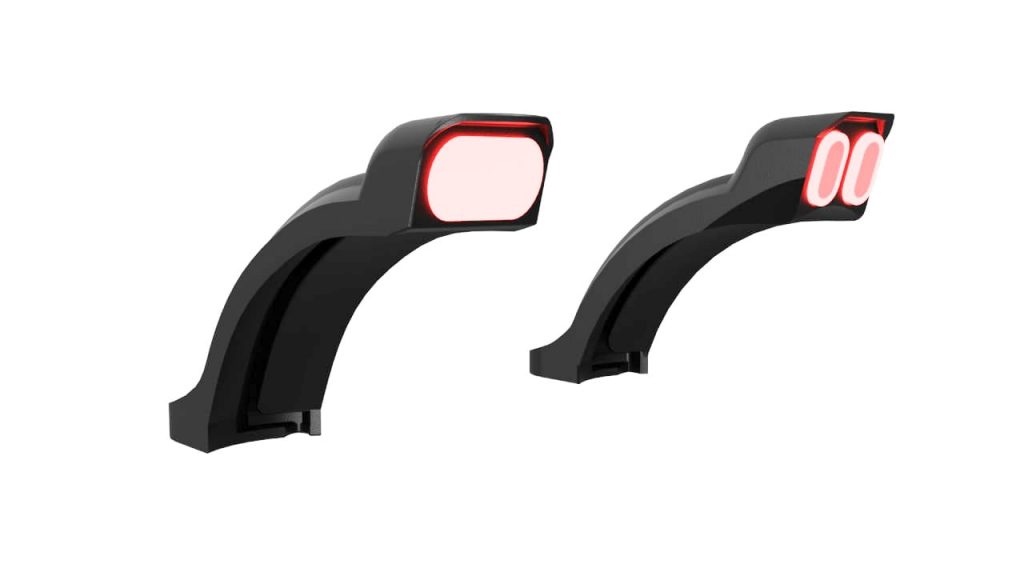
Fase 3 – Configurazione stampante FDM
Una volta convinti dei disegn dei prodotti Mi Customs siamo passati a tutto ciò che riguarda la preparazione della stampante, dalla scelta dei suoi upgrade alla scelta del filamento.
Come precedentemente citato per la creazione dei prodotti ci siamo affidati ad una stampante FDM, la quale va a creare oggetti depositando sottilissimi strati di plastica fusa passaggio dopo passaggio. Dettaglio da non trascurare: le stampanti FDM non sono come le classiche stampanti ad inchiostro dove una volta collegata la stessa alla porta USB del PC si è pronti a stampare. Esse richiedono varie calibrazioni sia hardware sia tarature software a seconda del tipo di materiale che si va a stampare (flusso di stampa, retrazioni, temperatura di stampa, accelerazioni, jerk). Questo è proprio uno dei motivi per i quali molti neofiti stampatori 3D abbandonano ai primi insuccessi.
Altro parametro è la scelta del piatto di stampa. Un prodotto, come un parafango ad esempio, va stampato partendo da un lato dello stesso. E’ quindi necessario selezionare una superficie che permetta una buona adesione (il primo strato deve letteralmente incollarsi sul piatto caldo di stampa) ma al contempo che dia una finitura quanto più simile a quella dell’ultimo strato superiore, onde evitare di creare disomigeneità visto che entrambi i lati saranno ben visibili nell’utilizzo quotidiano.
Nel nostro caso abbiamo optato per una superficie in PEI nella sua versione Smooth (vedi foto), finitura discetamente liscia ma non il classico effetto “specchio” del vetro. Per il cupolino, la quale base non è in primo piano una volta montato, abbiamo optato per un PEI Textured.
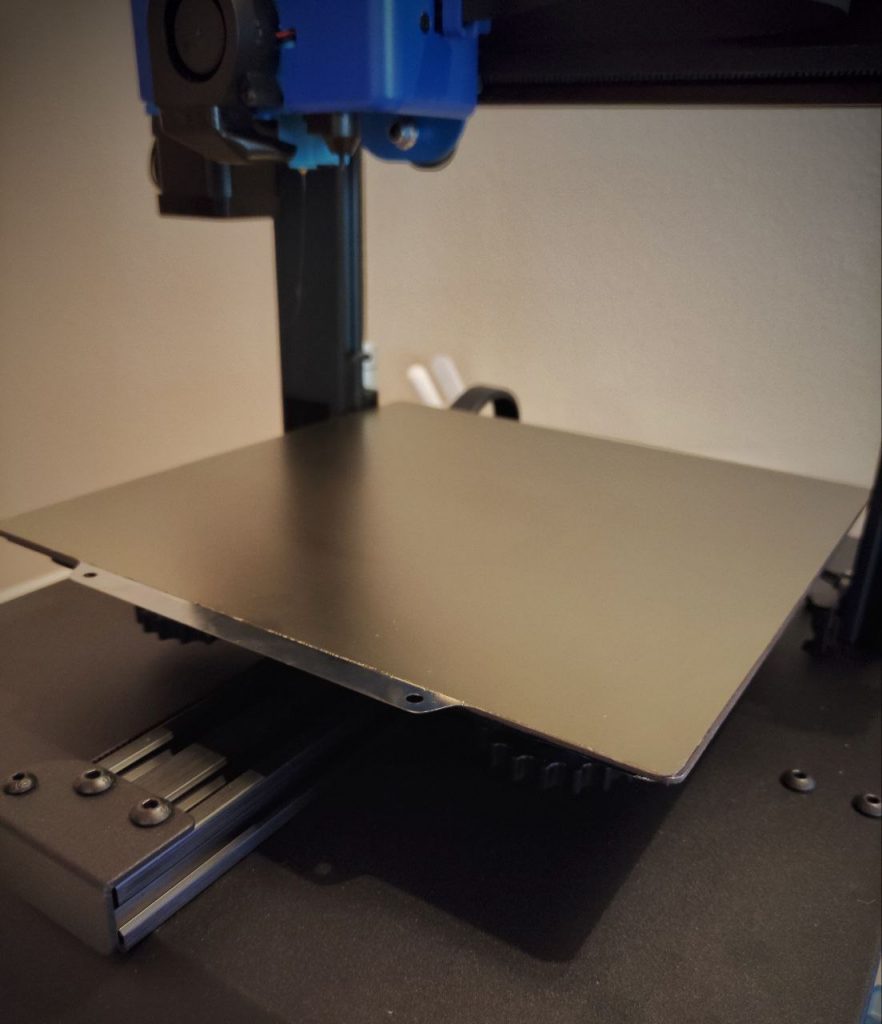
Parametro fondamentale ed altamente oculato per la stampa dei prodotti Mi Customs è la scelta del materiale di stampa: il filamento. I filamenti stampabili con tecnologia FDM sono svariati: PLA, PLA+, PETG, ASA, ABS, TPU ecc. Ogni materiale possiede le sue doti di finitura, adesione tra layer, resistenza meccanica, resistenza alle alte temperature, lucidità.
Nel nostro caso abbiamo optato per il PETG: stampabile senza grosse difficoltà, buona resa estetica, alta adesione tra singoli strati (il componente non deve “sfogliarsi”), buona resistenza alle alte temperature e meccanica (il parafango deve reggere il peso del monopattino quando chiuso). Abbiamo provato vari marchi, prodotti prettamente in cina: per trovare il prodotto che soddisfi le nostre esigenze siamo però rimasti nella nostra cara europa.
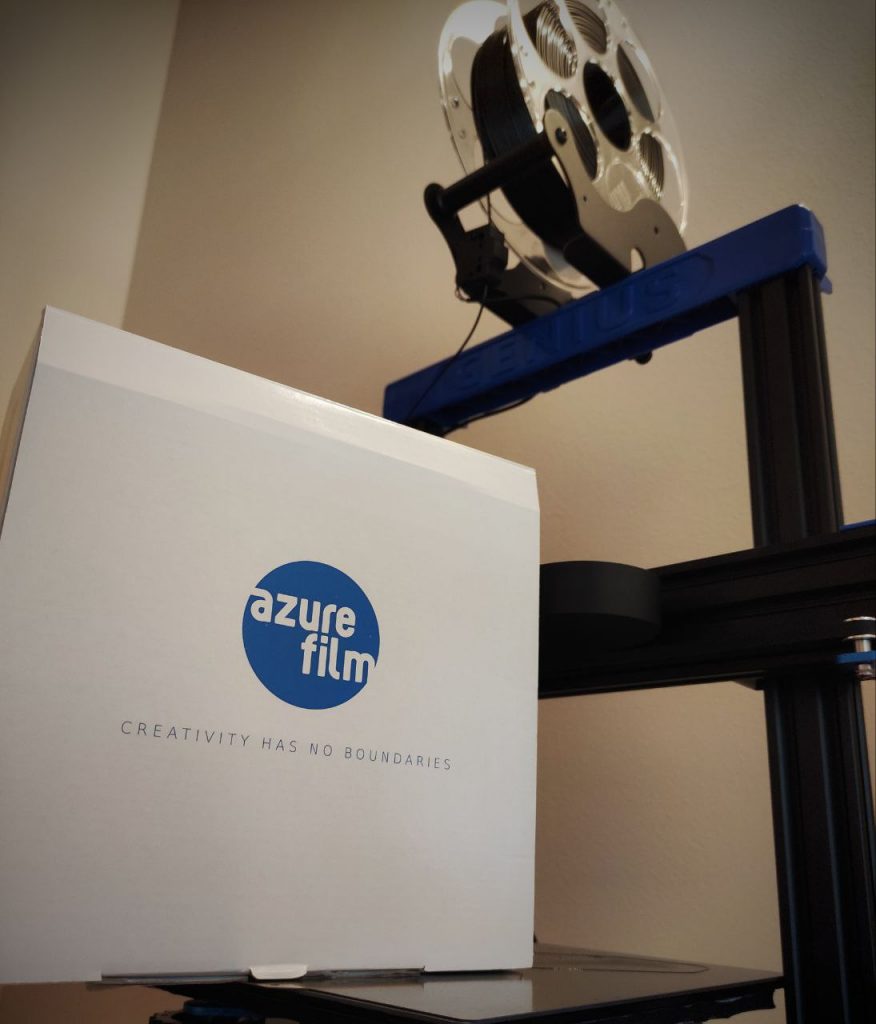
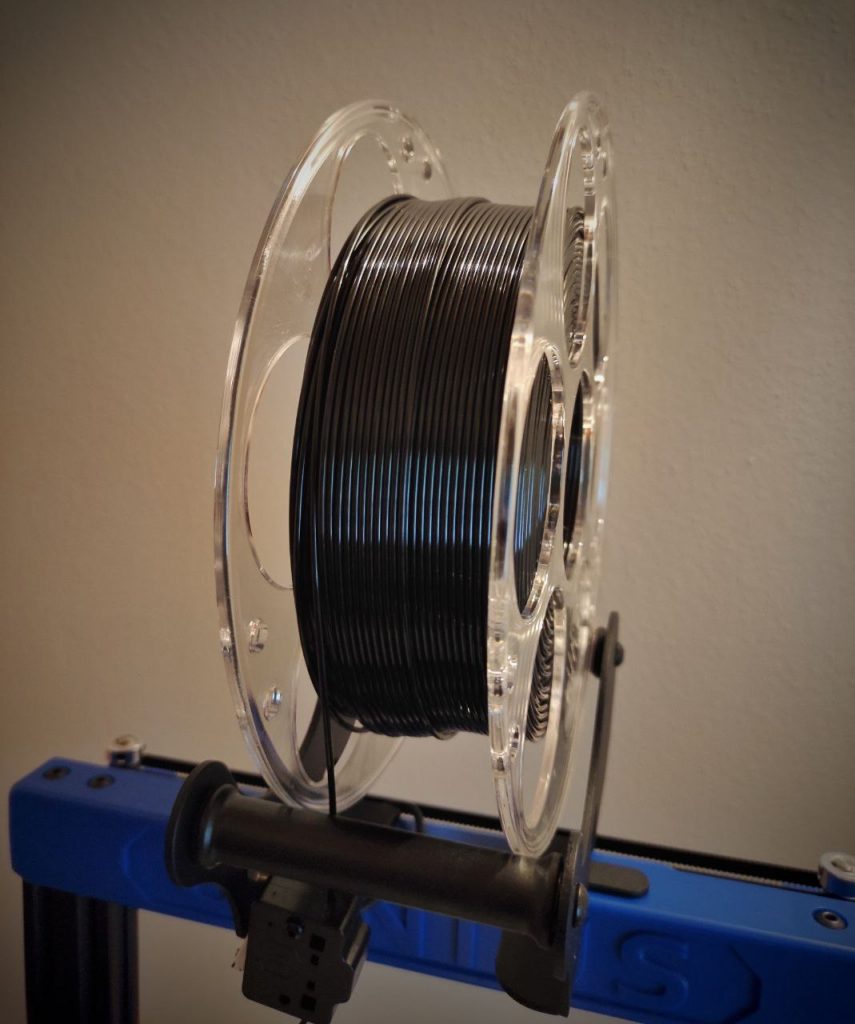
Abbiamo poi sostituito il classico ugello in ottone stock da 0,4 mm con un ugello di qualità superiore e di diametro leggermente maggiorato (0,5 mm): un foro più grande permette una fuoriuscita più omogenea di materiale e permette di depositare strati più spessi conferendo maggior resistenza al pezzo stampato.
Fase 4 – Slicing
Dopo aver configurato in maniera ottimale la stampante siamo passati alla fase di slicing: tramite software dedicati il file STL viene convertito in un linguaggio interpretabile dalla stampante, dandole direttive su estrusioni di materiale, movimenti, velocità, temperature. Procedura immediata? Assolutamente no ovviamente!
Tramite lo slicing si impostano svariati parametri tra cui ad esempio:
- Velocità di stampa: il PETG non gradisce stampe veloci. Esso necessità di un po’ di tempo per raffreddarsi ed aderire allo strato inferiore. Passare sopra ad uno strato non ancora ben stabile porterebbe a stampe di scarsa qualità.
- Temperatura di piatto ed ugello: una corretta temperatura del piatto permette un’ottima adesione del primo strato del pezzo. Un pezzo che si stacca o si solleva è immediatamente da buttare. La temperatura dell’ugello invece è strettamente correlata a stampante e materiale di stampa. Stampe troppo fredde porterebbero a scarsa adesione tra layer, mancanze di estrusione. Temperature troppo alte a “colature” e bolle in tutta la stampa. Le temperature di stampa del PETG si aggirano tra i 215 e i 240°, individuare il parametro perfetto in questo range ha richiesto svariati test.
- Ventilazione: la stampante dispone di una ventola che soffia aria sullo strato appena depositato. Il PETG gradisce ventilazioni basse, soprattutto se quel che si cerca è la resistenza. Una bassa ventilazione permette ai vari strati di fondersi correttamente tra di loro.
- Altezza layer: altezza di ogni singolo strato depositato. Layer alti permetterano stampe più veloci ma con strati più visibili. Layer sottili permetteranno un’altissima resa estetica ma stampe con tempi biblici.
- Perimetri, riempimento: i perimetri sono gli strati pieni della parte più esterna della stampa, rappresentato il guscio della stessa. Essi conferiscono solidità al pezzo stampato. Il riempimento è ciò che è all’interno del pezzo e dona ulteriore resistenza. Occorre raggiungere un compromesso tra resistenza del componente e consumo di materiale e tempi di stampa. Riempimenti eccessivi comporterebbero scarsoi aumenti di resistenza in relazione a costi del materiale usato e tempo di stampa.
Tutti i parametri vanno quindi valutati in correlazione della stampante, materiale e utilizzo del prodotto finale.
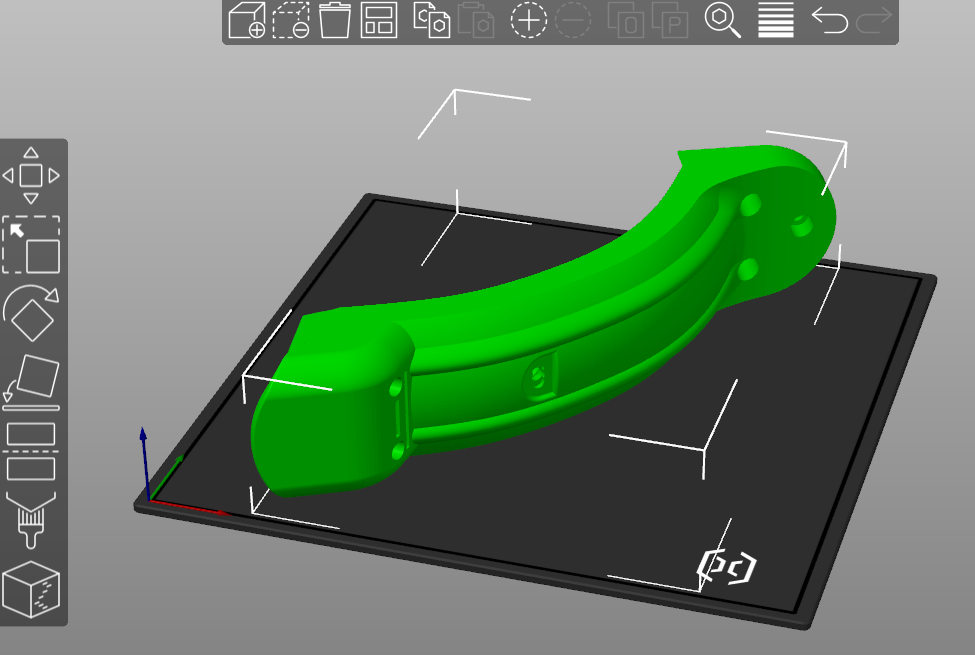
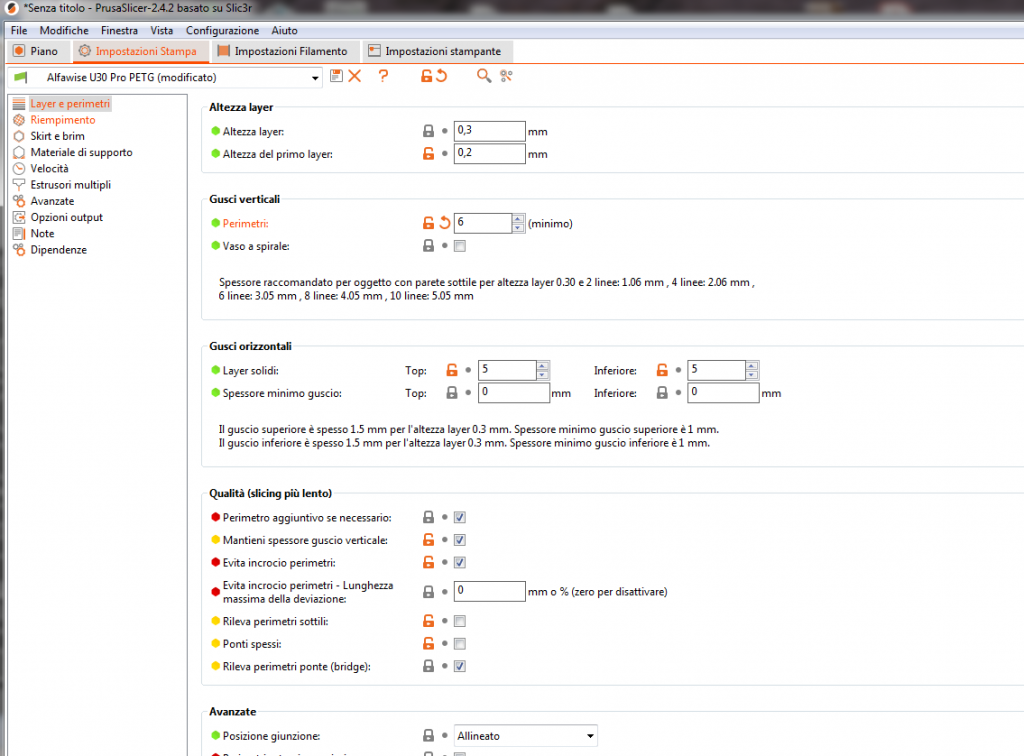
Fase 5 – Stampa
Eccoci in quella che è l’ultima fase di questo lungo processo. Il File GCODE viene caricato nella stampante, generalmente tramite un supporto SD o USB.
Essendo la stampa un processo duraturo (svariate ore) e non essendo esente da errori, non ci piace assolutamente lasciar andare il tutto senza un minimo controllo su di essa. Stoppare precocemente una stampa che sta venendo male permette risparmio di tempo e di materiale. La macchina lavora inoltre ad alte temperature: i casi di incendio, seppur rari, hanno colpito più di qualche stampatore 3D.
A venirci incontro a questo ci pensa prima di tutto una piccola videocamera WiFi HD con visore notturno la quale, puntata sul piatto di stampa, ci permette di tener sotto controllo il tutto anche se non presenti nel locale ove risiede la stampante.
Altra “chicca”è stata lo sfruttare uno smartphone Android con schermo frantumato per usarlo come server di stampa, rendendoci possibile anche il caricamento dei file GCODE via rete Wi-Fi. Collegato alla stampante tramite presa OTG e cavo USB su HUB alimentato (altrimenti lo spegnimento dello smartphone per batteria scarica stopperebbe la stampa a metà), tramite l’app Octo4a (Octoprint for Android) possiamo avviare stampe, monitorare e variare le temperature, stoppare le stesse in caso di errori, verificare a che punto è arrivato il processo. Tale software è nato per sistemi di tipo Raspberry ma visti i costi esorbitanti di questi mini pc tanti stampatori si sono convertiti all’utilizzare vecchi (o semi rotti) smartphone, noi compresi.
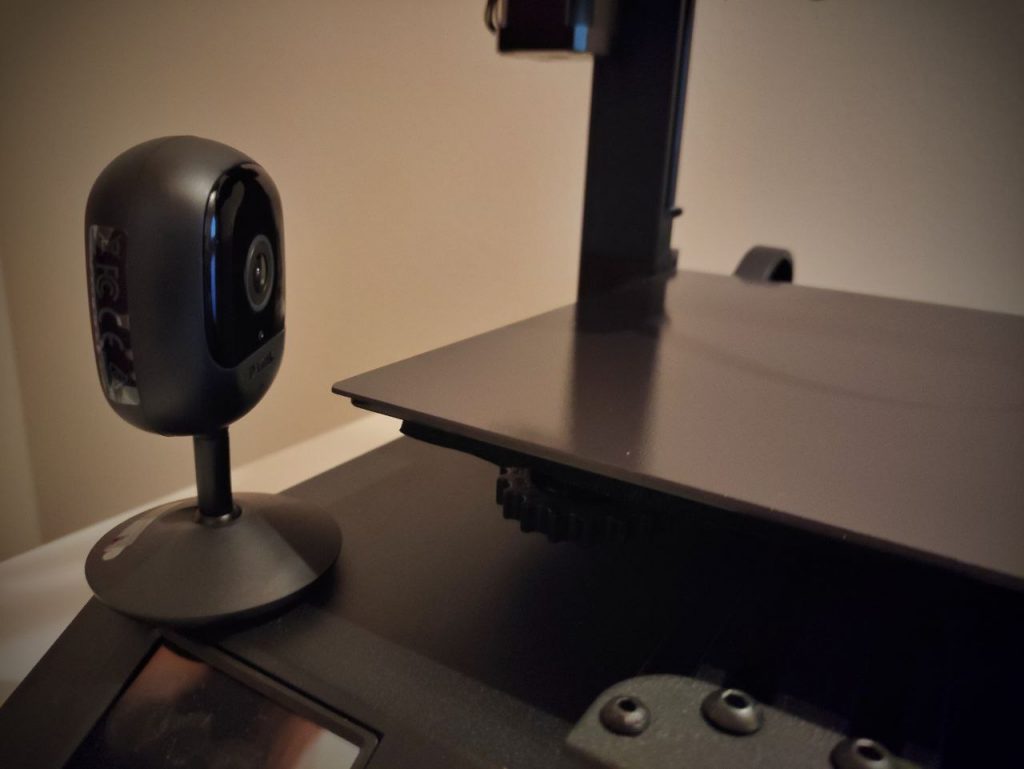
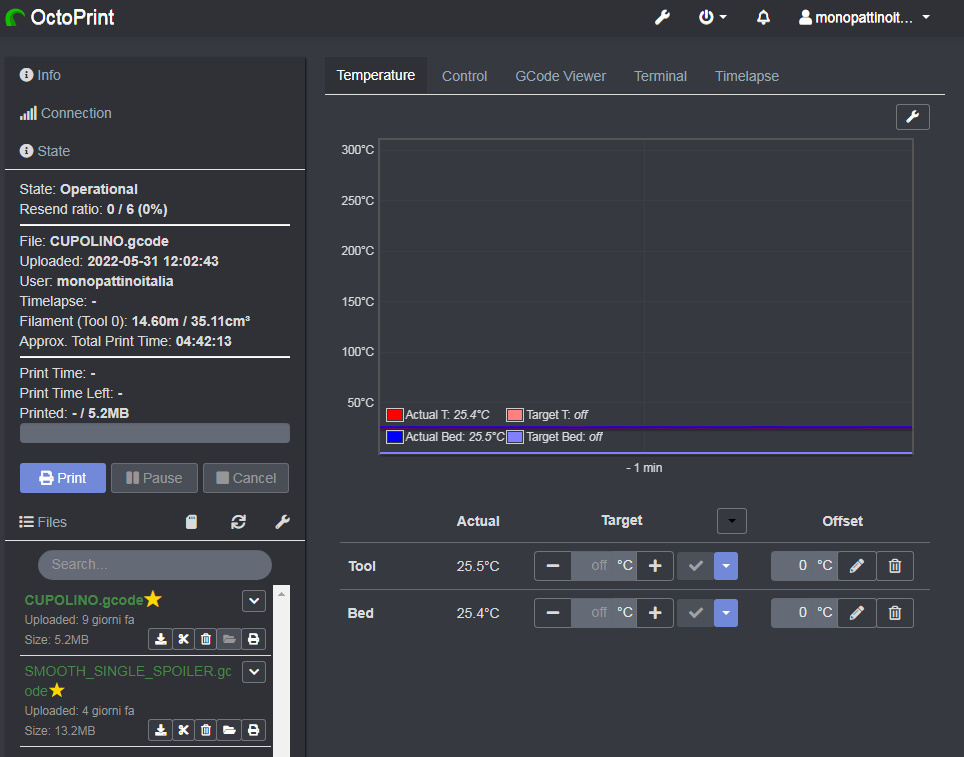
Il processo di stampa di un parafango Mi Customs dura tra le 9 e le 10 ore circa.
Fase 5 – Il prodotto finale
Veniamo ora alle foto dei prodotti da noi completamente progettati e stampati. Ricordiamo che nonostante il nostro massimo impegno e studio dei parametri di produzione, l’utilizzo della tecnologia di manifattura additiva comporta il fatto che essi non sono esenti ad imperfezioni, piccole sbavature e tracce di layer visibili. Ogni parafango è stato totalmente disegnato e prodotto da noi e rappresenta un pezzo unico nella sua imperfezione.
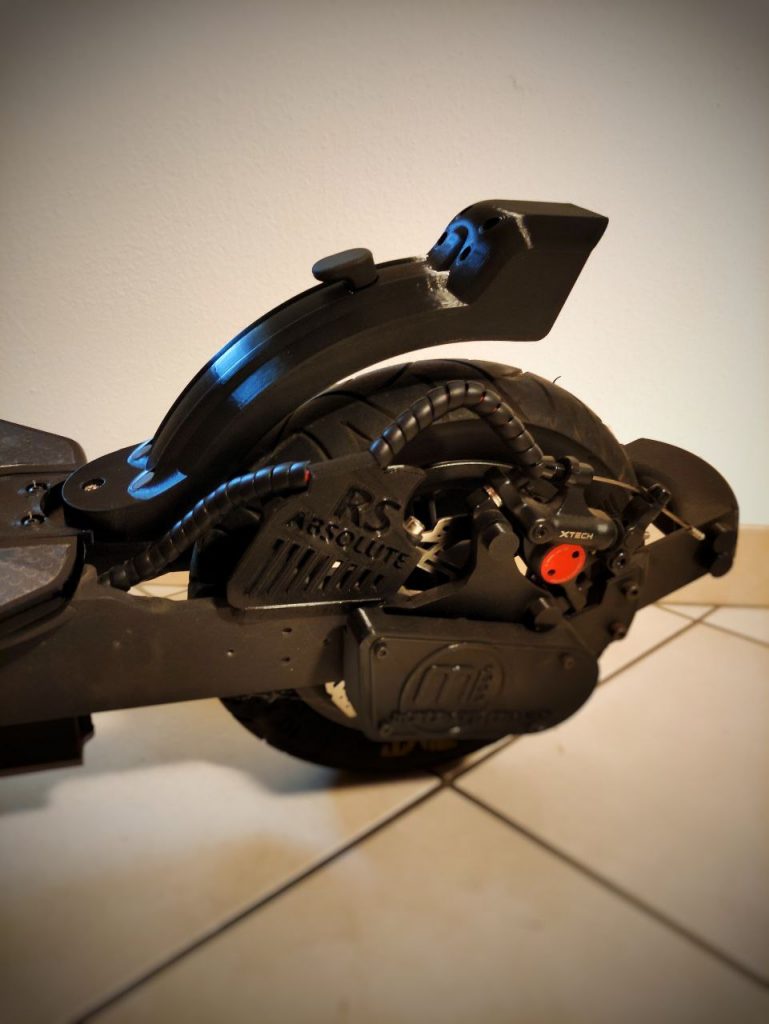

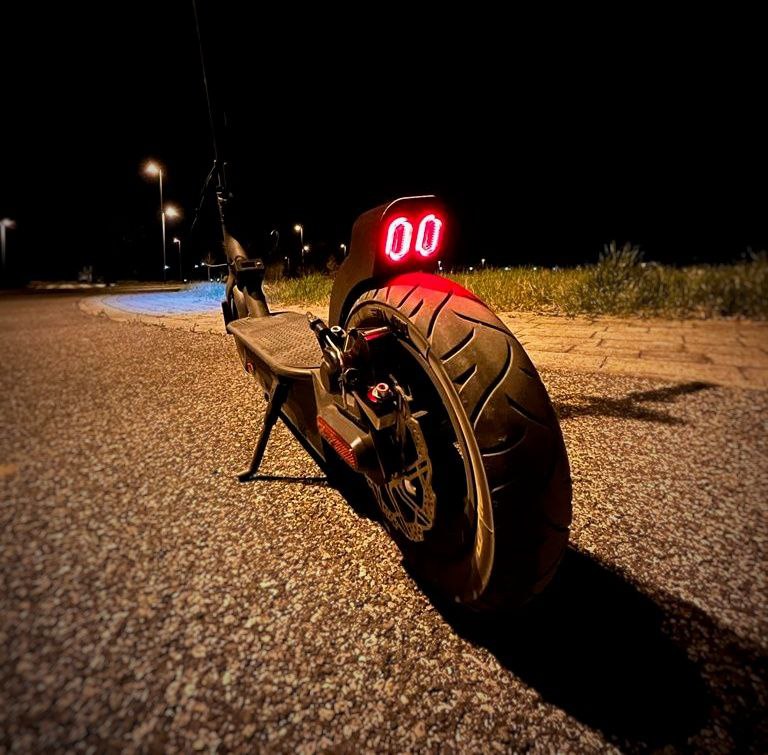
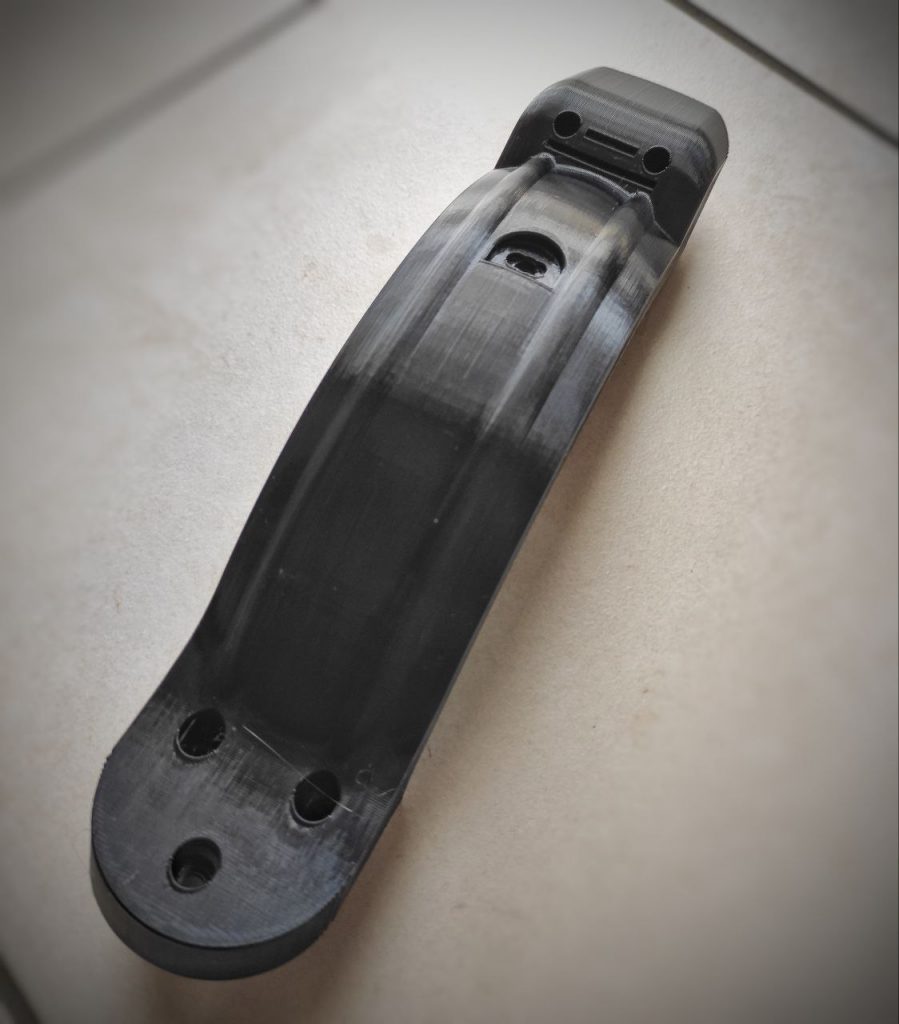
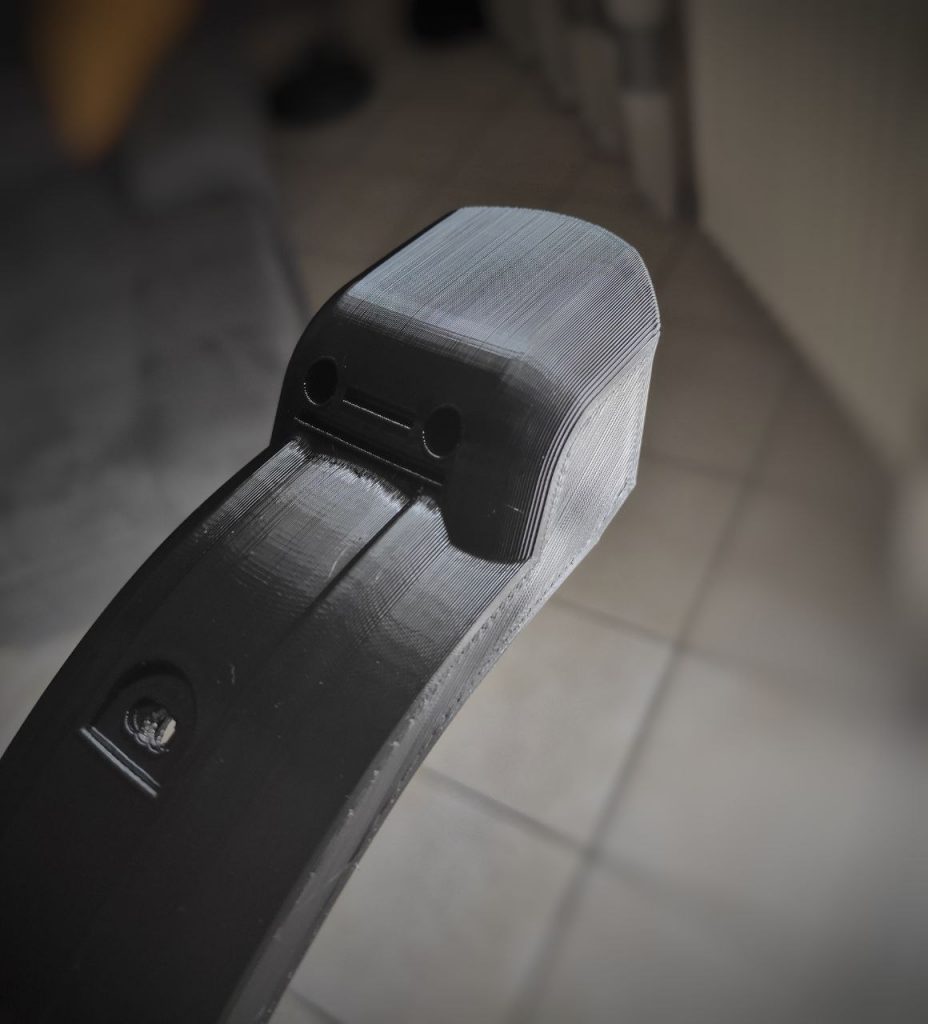
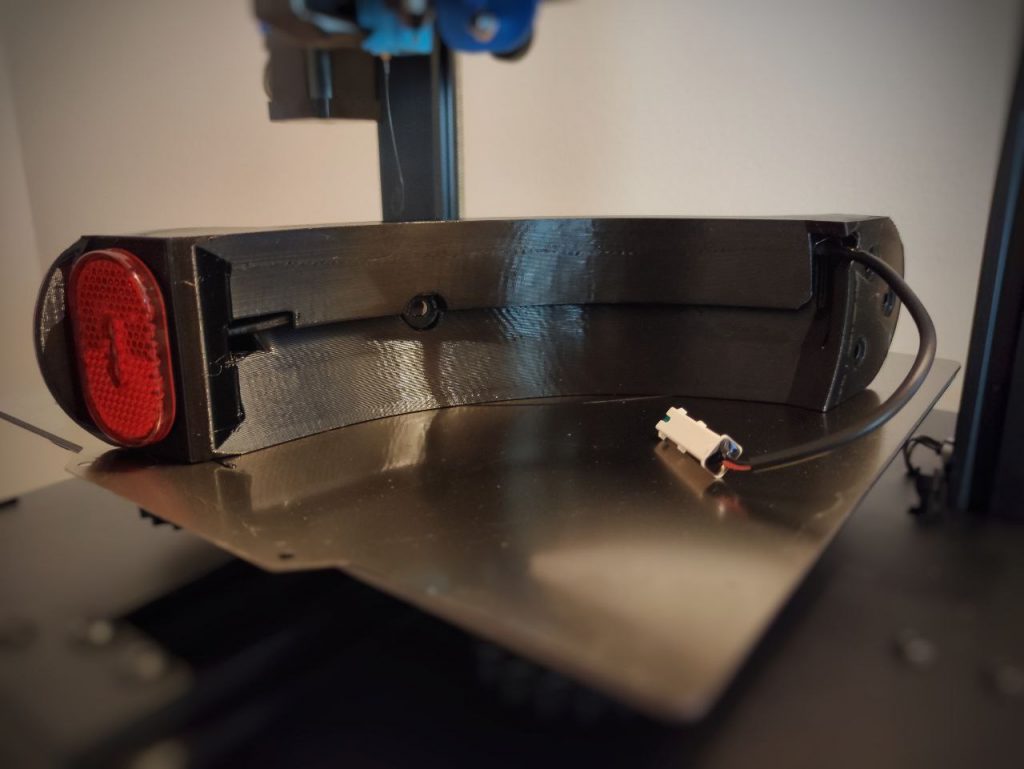
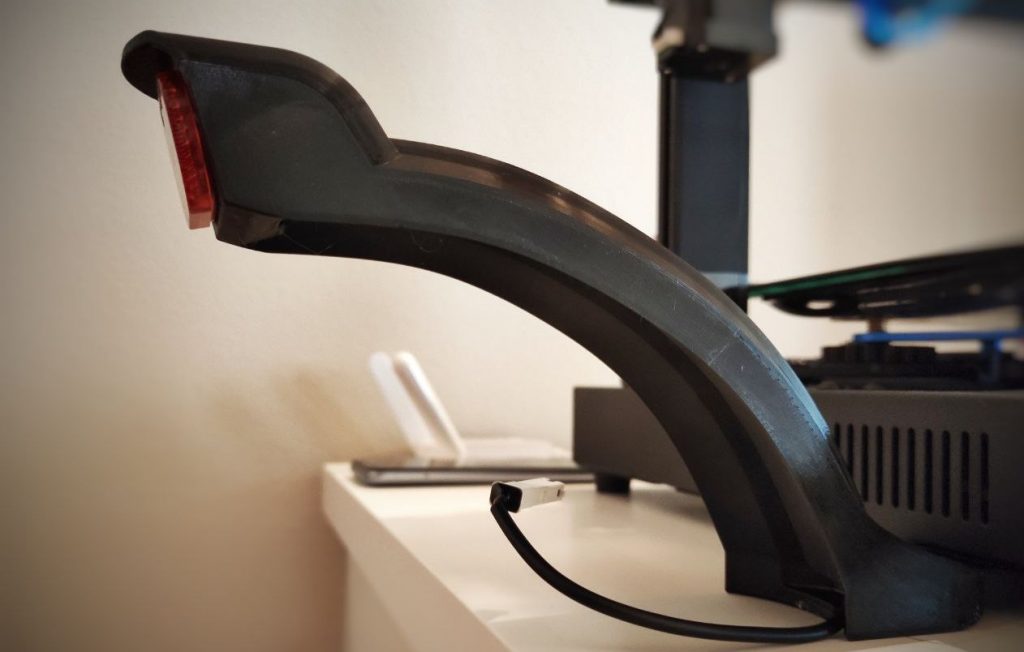
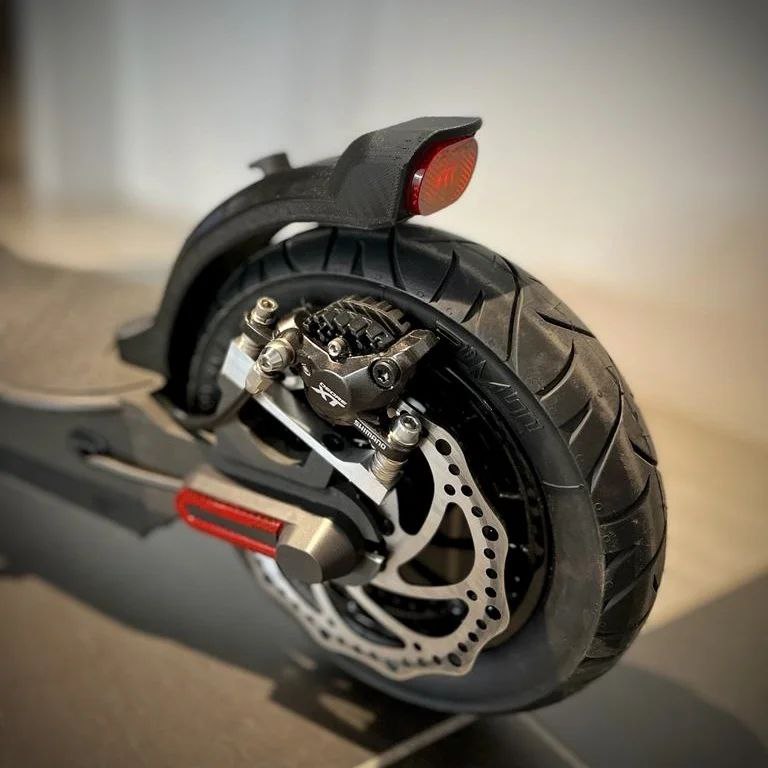
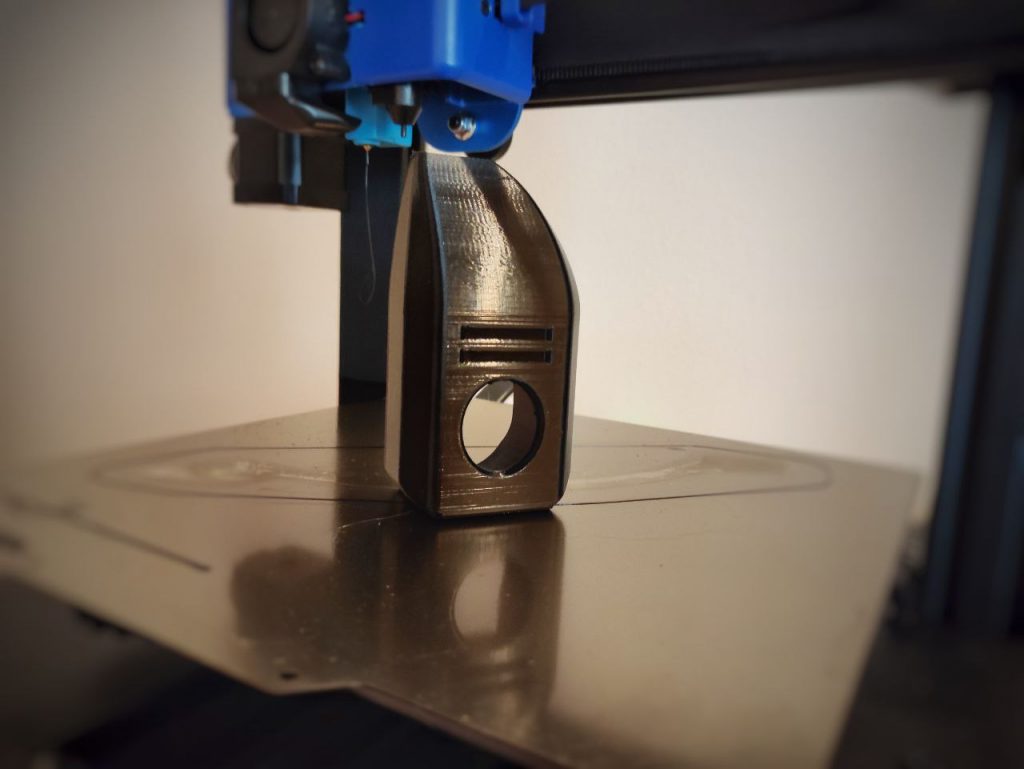
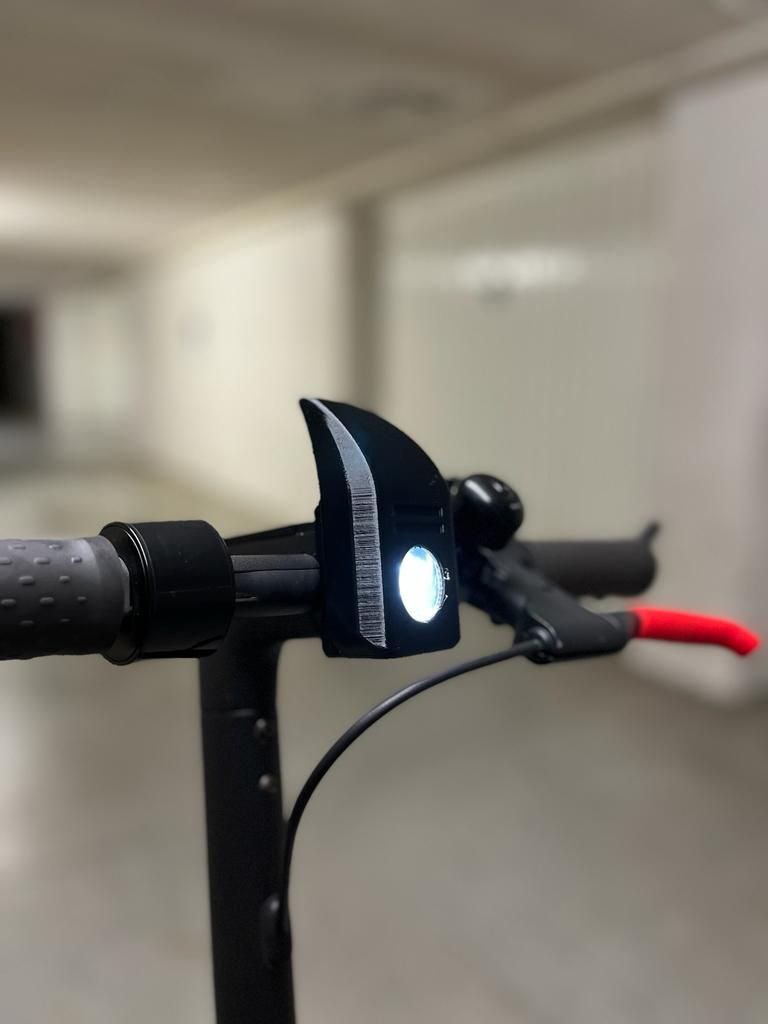
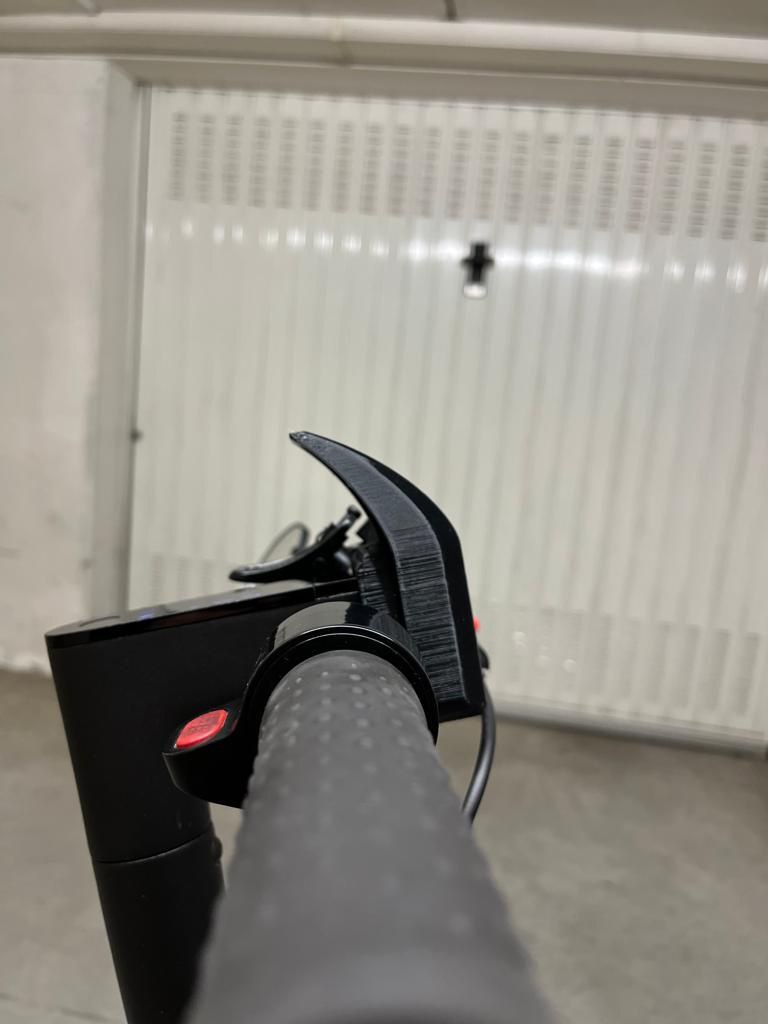
Tali parafanghi sono progettati per una completa compatibilità per gomme da 10″ senza bisogno di rialzi o staffe laterali come quelle presenti sul parafango originale. Il cavo del fanale verrà lateralizzato sul canale presente al lato DX del monopattino per evitare che esso vada a strisciare sullo pneumatico.
Essi sono prodotti in quantità limitata, non siamo una azienda e non ci è possibile ne troviamo giusto produrne grandi stock.
Vengono forniti senza fari e ganci di chiusura. E’ infatti possibile riciclare quelli presenti sul parafango originale Xiaomi. Ovviamente il parafango Smooth Dual richiederà due fanali Xiaomi prima serie, facilmente reperibili online (link presente nella pagina di acquisto dei parafanghi).
Scusate il nostro essere prolissi ma abbiamo trovato corretto (anche verso i più curiosi) spiegare cosa c’è dietro ogni singolo pezzo nonchè fornire una infarinatura di quella che è la stampa 3D!
Sei interessato all’acquisto? Puoi acquistare i parafanghi MI CUSTOMS cliccando qui! Il cupolino non è attualmente in vendita!